
Fun with Fussy-Cutting
- Beth Ann
- June 30, 2023
- Quilting
- Sewing
- Technique Tutorials
I’ve been working on a new bed quilt lately; and as I’ve been cutting my fabric, I’m starting to accumulate quite a pile of new scraps. I started setting some of the scraps to one side. I had an idea… Fussy-cutting is a fun way to feature a specific design or motif in a fabric […]
Read More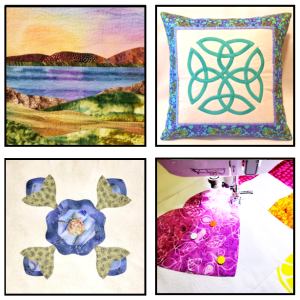
A Few of My Most-Used Tools & Notions for “Invisible” Machine Appliqué
(Updated April 2024) With new sessions of the Modern Rose, The Magic of Invisible Machine Appliqué, Create Your Own Quilted Landscape, and the Celtic Blessings True Lovers Knot Invisible Machine Appliqué classes coming up in my online shop, I thought it might be a good time to share a few of my most-used (and most […]
Read More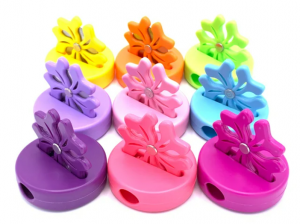
A Few of My Favorite Things
I still have that catchy tune from the movie A Sound of Music stuck in my head, so I thought it might be fun to start a sewing & quilting themed list of A Few of My Favorite Things. These are in no particular order, and they are not paid endorsements from the companies involved […]
Read More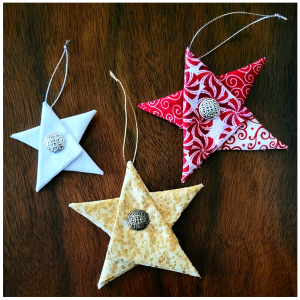
FREE PROJECT – Fast & Fun Folded Fabric Stars
These scrap-busting stars make great holiday ornaments or decorations, and are easy enough that kids can enjoy making them, too. 😊 What You’ll Need: 3 strips of fabric for each star I used 3” x 10” strips for the larger stars and 2” x 7” strips for the smaller star. You can use 3 strips […]
Read More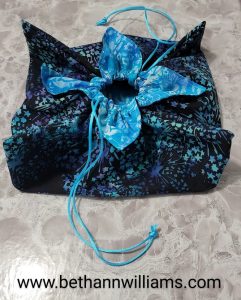
FREE Project – Origami Drawstring Bag
I have a quick and easy photo tutorial for you today – along with some fun photographs from when Connor and I taught this project in the Kids Make It, Take It classes we used to offer through Lakeshore Sewing. Not only is this delightful, giftable little bag useful and appealing for all ages – […]
Read More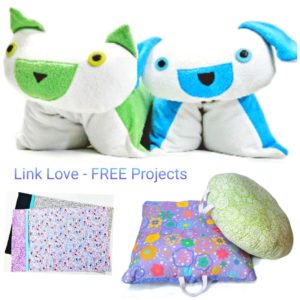
Link Love – 4 FREE Projects for the Young & Young at Heart
- Beth Ann
- January 31, 2022
- FREE Projects
- Link Love
- Reviews
- Sewing
The cold snowy weather we’ve been having lately is perfect for staying in and sewing – and if your weather as been anything like ours, you may have some kids or teens at home, too. So I’ve rounded up a short list of free projects and tutorials that my daughter Connor and I have tried […]
Read More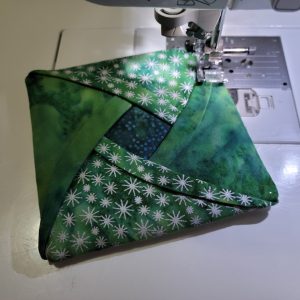
FREE Project – Festive Holiday Coasters
Hello again, everyone! As some of you know, I went through a cancer scare this fall, and had my hands more than full with doctor visits and subsequent surgery a couple of weeks ago. But I am thrilled to report that my final biopsies came back negative & I’m getting my groove back! I have […]
Read More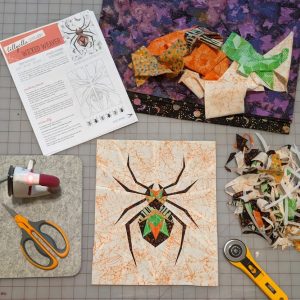
Wicked Weaver & My New Favorite Product
The October Java Batiks box from Cotton Cuts and the Midnight Bite Sew Along (#MidnightBiteSAL) from Lillyella Stitchery offered me a fun opportunity to go outside my comfort zone this month. The Midnight Bite pattern bundle has 3 sizes of each of two different patterns – a bat and a spider. I opted to make […]
Read More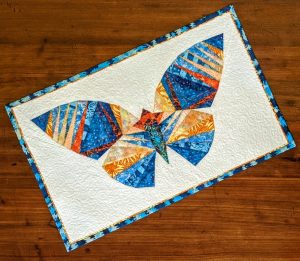
Finishing Spree – Take Wing, Foundation Piecing, & Mixing Quilting Methods
Foundation piecing (also called foundation paper piecing) is a great technique for achieving precise piecing and sharp points even with tiny pieces and fabric edges that are not on-grain. For this method, the pattern is printed (or traced) onto foundation paper. This paper acts as both a stabilizer and a stitching guide while the block […]
Read More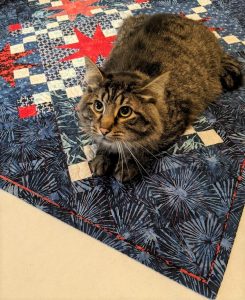
Finishing Spree! Fireworks, Curvy Quilting & “Disappearing” Binding
I haven’t been posting much this summer, but I’ve certainly been sewing up a storm! I’m finding it good therapy. 🙂 Due to the pandemic, we weren’t able to enjoy our usual fireworks display downtown this year, but I was inspired by the July Java batiks box from Cotton Cuts to create some fireworks of […]
Read More