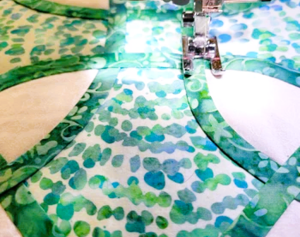
Beautiful Celtic Appliqué by Machine – Appliqué and Quilt in One Step
If you’ve ever been captivated by the intricate beauty of Celtic knotwork but wondered how to bring that into your quilting – this one’s for you. In this video, I’m sharing my favorite method for machine-stitched Celtic appliqué, including: To demonstrate each step, I’ll walk you through the process I use when creating the Celtic […]
Read More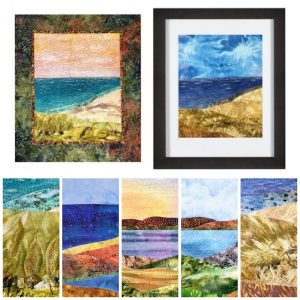
Choosing Fabrics for a Quilted Landscape
- Beth Ann
- February 11, 2025
- Classes
- Quilts
Since my Create Your Own Quilted Landscape class is coming up quickly (listed here in my shop). I thought I’d reshare some of the fabric selection tips I included in last week’s email newsletter. This machine appliqué-and-quilt in 1 step project is much easier than you probably think! Whether you use my tips to draw […]
Read More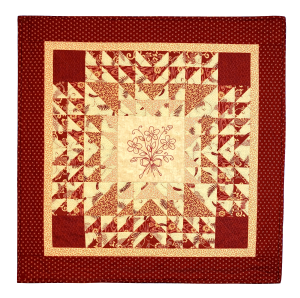
Quilting Legacies and Quilt Labels
- Beth Ann
- November 20, 2024
- Quilts
- Technique Tutorials
Even as we grieve her recent passing, we’re taking great comfort in wrapping up in quilts made by my mother-in-law Sue Williams, and reflecting on how much joy quilting – and giving quilts to those she loved – gave to her. However, one thing I wish she had done differently is take the time to […]
Read More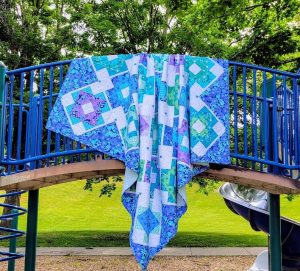
A Quilt for Myself – Adapting the Meadowland Quilt Pattern
- Beth Ann
- June 4, 2024
- Color & Value
- Quilting
- Quilts
- Reviews
Like most quilters I know, I am much more likely to prioritize a quilt I am making as a gift or as a class or pattern sample than a quilt I am making purely for my own use. Do you do that, too? But last week, I gave myself the gift of a few days […]
Read More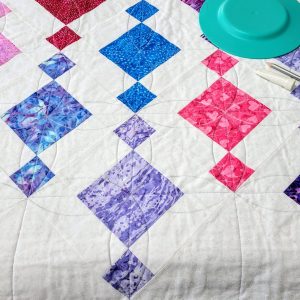
Walking Foot Quilting for My Beads/Chandelier Quilt
In my last post, I shared my progress on my Beads or Chandelier quilt, along with a free pattern from Donna Jordan of Jordan Fabrics. Today, I plan to share with you how I’m machine quilting my quilt on my home sewing machine with a walking foot. I spray basted my quilt sandwich with 505 […]
Read More
Link Love – The Beads or Chandelier Quilt
Free patterns are always fun, aren’t they? Well, today I have a delightful pattern recommendation to pass along to you: a pretty, on-point Beads quilt pattern by Donna Jordan from Jordan Fabrics. There’s even a video to go with the pattern! Scroll down the page to see the video. Here’s what inspired this project – […]
Read More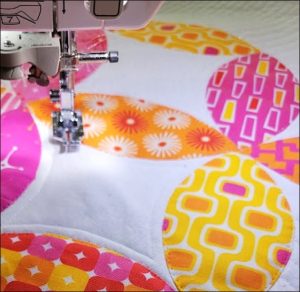
Easy & Elegant Echo Quilting
Machine quilting doesn’t need to be fussy, difficult, or complicated to be effective (Although over-the-top quilting can certainly be gorgeous!) One of my favorite techniques that is also super-easy and beginner-friendly is echo quilting. Echo quilting is simply choosing a seam in a pieced quilt or the edge of an appliquéd shape and stitching parallel […]
Read More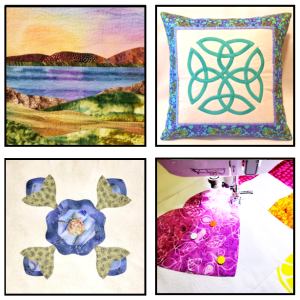
A Few of My Most-Used Tools & Notions for “Invisible” Machine Appliqué
(Updated April 2024) With new sessions of the Modern Rose, The Magic of Invisible Machine Appliqué, Create Your Own Quilted Landscape, and the Celtic Blessings True Lovers Knot Invisible Machine Appliqué classes coming up in my online shop, I thought it might be a good time to share a few of my most-used (and most […]
Read More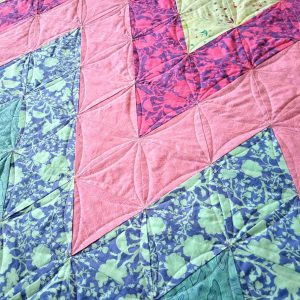
The Heatwave Quilt & Bringing Back Continuous Curve Machine Quilting
- Beth Ann
- April 3, 2023
- Machine Quilting
- Quilts
- Reviews
I recently had the opportunity to test another fun pattern from Tied with a Ribbon – the Heatwave Quilt. I haven’t really played much with equilateral triangles in the past, so I was eager to try something new. And it did not disappoint! You can read about my adventures constructing this quilt with the aid […]
Read More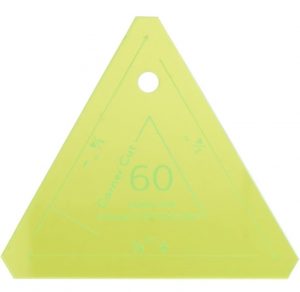
The Corner Cut 60
- Beth Ann
- January 30, 2023
- Quilting
- Quilts
- Reviews
I’m tickled to be pattern-testing another wonderful new pattern from Jemima of Tied with a Ribbon. I can’t show the full Heat Wave quilt until the official pattern release a little bit later this spring, but I can show you some in-progress pics and a GREAT tool I’ve discovered for working with 60 degree (equilateral) […]
Read More