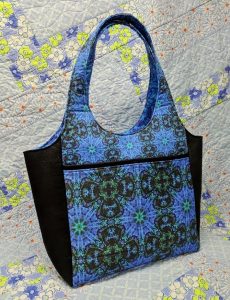
Link Love – Cork and the Clydebank Tote
Have you ever heard of cork fabric? I was dimly aware of it, but it hadn’t really registered for me as something I’d like to try until I came across this post on the Sew Sweetness blog by Sara Lawson. In conjunction with an online book club she is hosting, Sara is posting a free […]
Read More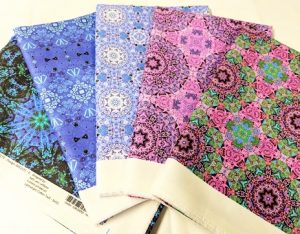
Checking Out Lightweight Cotton Twill
So I’m in love with the Kona Cotton Ultra from Spoonflower.com – it’s my go-to fabric choice when ordering, but when the site ran a promotion on Lightweight Cotton Twill, I took a chance and ordered some. I’m so glad I did! I find the lightweight cotton twill launders well, is super easy to work […]
Read More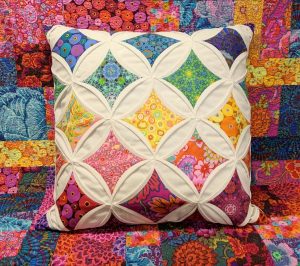
Link Love – Fun with Cathedral Windows
Cathedral windows has been a favorite pattern of mine since I first saw this traditional quilt style many years ago, but I’ve never made more than a few blocks at a time because the handwork proved too frustrating for me to manage wth my peripheral neuropathy. So I was immediately intrigued when I heard about […]
Read More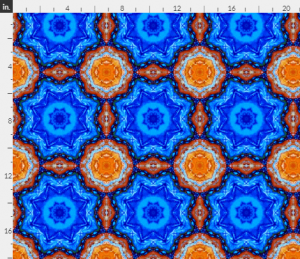
Out of My Comfort Zone – Desert Modernism Challenge
Why do I love Spoonflower so much? As an independent designer (as well as consumer), I get a terrific way to create custom textiles for my own use, as well as to sell 20+ different types of fabrics (plus wallpaper, gift wrap and ready-made home decor items) printed with my original artwork to designers and […]
Read More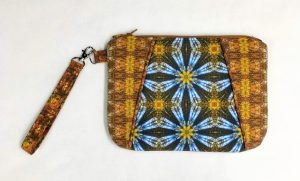
Adding Structure with Soft and Stable – Review & Tips
One of the really great things about sewing is that you aren’t dependent on what you can find (or afford) in the store – you can create or customize all kinds of things to your specific tastes and needs. Lately, I’ve been on a streak of making totes, bags and purses. Since my work (both […]
Read More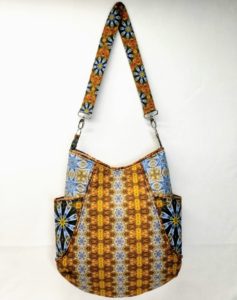
The 241 Tote from Noodlehead – Review, Part 2
As anyone who sews or quilts can tell you, individual patterns have gotten more and more expensive over the years, especially if you like to seek out and support independent designers. Being able to download patterns and save them as pdfs can help (as opposed to buying printed patterns, with or without paying additional for […]
Read More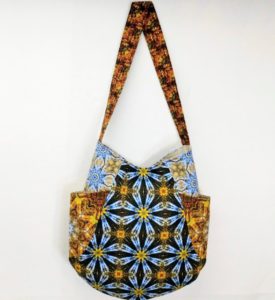
The 241 Tote from Noodlehead – Review, Part I
Did you ever experience a breathless moment in time when you looked up and knew in that brief instant that THIS was THE ONE? Ok, let’s get our minds back on track here… I don’t know what you are thinking about, but I’m talking about tote bags. 😉 I love totebags. Cute little purses just […]
Read More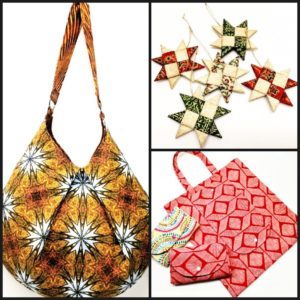
December Wrap-Up & Link Love
What a month! Not only is late November through December extra-busy with the holidays AND one of the most demanding times of the year for my day job as Creative Director for Lakeshore Sewing, but our plumbing saga continued with more water in the basement, where my studio is located. Needless to say, my creative […]
Read More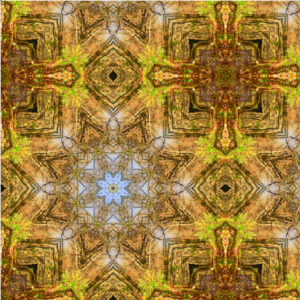
Adventures with Spoonflower – Changing Seasons
In my last post, I shared the origins of my Around the World and Back Again collection. This time, I’d like to share a bit of the inspiration behind the designs in my collection Changing Seasons. For several years, my dear friend June Mears Driedger and I co-hosted Storytelling in Fiber retreats at the Hermitage […]
Read More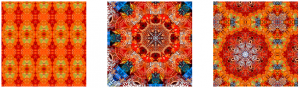
Adventures with Spoonflower – Around the World and Back Again
I haven’t been posting lately, but I HAVE been creating. 🙂 Working on designs for a couple of new fabric collections has made me reflect a bit on previous work. Today I thought it would be fun to revisit the first fabric designs I ever uploaded to my shop on Spoonflower.com. Around the World and […]
Read More