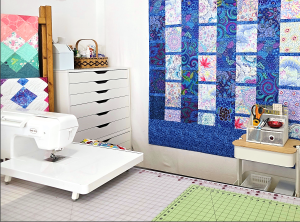
Creating a Movable Quilting Studio with IKEA Storage Solutions
- Beth Ann
- June 23, 2025
- Quilting
- Reviews
Is your sewing or quilting space temporary, shared, or constantly evolving? You’re not alone! Over the years, I’ve had to move my quilting setup from room to room depending on mobility needs, family needs, and available space. These days, my studio lives in one side of our dining room; and while it’s not a forever […]
Read More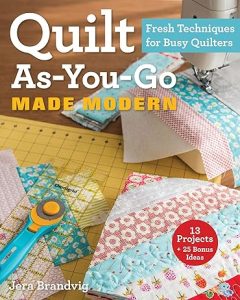
How Quilt-As-You-Go Made Modern Has Held Up After 10 Years
- Beth Ann
- June 10, 2025
- Machine Quilting
- Quilting
- Reviews
Wondering if Quilt-As-You-Go quilts really hold up over time? I revisited several quilts I made using Jera Brandvig’s QAYG method – where each block is quilted with batting (but no backing!) before being joined together. After 10 years of family use and frequent washing, I’m sharing what held up, what surprised me, and why I […]
Read More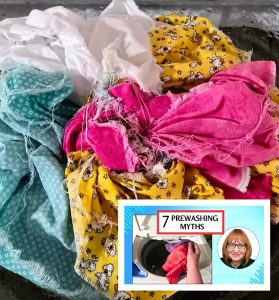
Myths and Truths About Prewashing: A Quilter’s Guide
- Beth Ann
- May 23, 2025
- Quilting
- Reviews
- Technique Tutorials
If you’ve ever Googled “Should I prewash quilting fabric?” you already know that the advice varies wildly. Some quilters insist on it. Others skip it completely. And plenty of us fall somewhere in between. In my newest video, I break down the most common myths and misconceptions around prewashing, including tips for dealing with fabric […]
Read More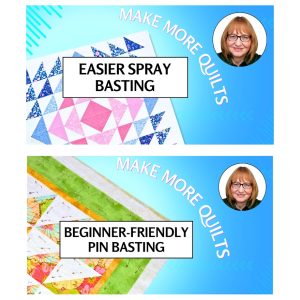
2 Different Approaches to Quilt Basting, Step-by-Step
I’ve talked about spray basting before, but I recently posted a FREE tutorial on my YouTube channel for those who wanted to see the process in more detail. But basting spray is not for everyone! Some folks find it too pricey or too difficult to source. Others may dislike the smell or would prefer not […]
Read More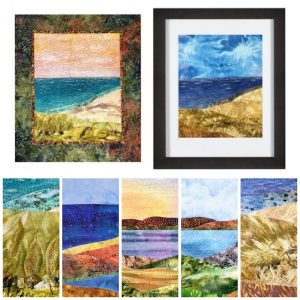
Choosing Fabrics for a Quilted Landscape
- Beth Ann
- February 11, 2025
- Classes
- Quilts
Since my Create Your Own Quilted Landscape class is coming up quickly (listed here in my shop). I thought I’d reshare some of the fabric selection tips I included in last week’s email newsletter. This machine appliqué-and-quilt in 1 step project is much easier than you probably think! Whether you use my tips to draw […]
Read More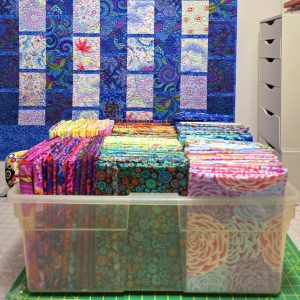
My Favorite Fabric Storage System (It’s not bins!)
- Beth Ann
- December 10, 2024
- Quilting
- Reviews
Read on if you would like to know more about how I buy fabric and the process I use for storing it. Just looking for links? Click here for the Comic Book Boards and click here for the plastic clips I am using. If you need more clips (like me), you can buy a larger […]
Read More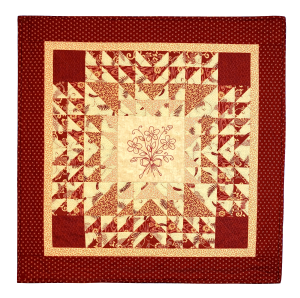
Quilting Legacies and Quilt Labels
- Beth Ann
- November 20, 2024
- Quilts
- Technique Tutorials
Even as we grieve her recent passing, we’re taking great comfort in wrapping up in quilts made by my mother-in-law Sue Williams, and reflecting on how much joy quilting – and giving quilts to those she loved – gave to her. However, one thing I wish she had done differently is take the time to […]
Read More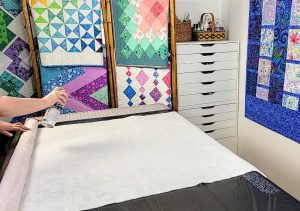
Quilt Basting with Pool Noodles and Broomsticks
I’m planning a series of posts with some of my favorite quilt basting tips. So, I thought I’d start by answering a question that recently came up in one of my machine quilting classes: “What are pool noodles and why do you like them so much?” Depending on the size of the quilt, the type […]
Read More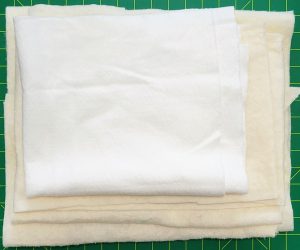
No-Waste Quilt Batting (Wadding)
If you’re like me, at some point you may find yourself with a pile of batting scraps in various sizes. I don’t like to throw these leftover bits and strips away; so I’ve developed a system that works well for me. I typically buy queen-sized packaged batting or 108″ wide batting on a roll and […]
Read More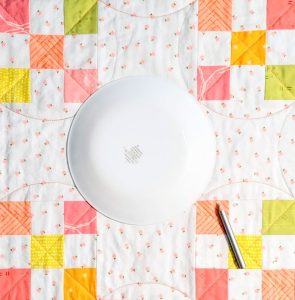
Quilt Marking Tools Update
Earlier this year, I shared the post Testing My Quilt Marking Tools. Since then, I’ve been putting my favorites to work on actual quilts, and I have some new info (and links) to share with you. One of the things that surprised me most both during the initial testing process and as I continued to […]
Read More